在現(xiàn)代制造業(yè)中,零部件缺陷可能會導(dǎo)致產(chǎn)品質(zhì)量問題和生產(chǎn)線效率下降。因此,零部件缺陷檢測成為了制造業(yè)中的一個重要環(huán)節(jié)。隨著科技的發(fā)展,人工智能、機器學(xué)習(xí)和計算機視覺等技術(shù)的不斷進步,零部件缺陷檢測技術(shù)也取得了長足的進展。本文將就該領(lǐng)域的進展和面臨的挑戰(zhàn)進行探討。
首先,現(xiàn)代零部件缺陷檢測技術(shù)已經(jīng)從傳統(tǒng)的人工目視檢查方式逐漸轉(zhuǎn)變?yōu)樽詣踊椭悄芑姆椒?。例如,基于計算機視覺和圖像處理的技術(shù)可以對零部件進行高速、精確的檢測和分類。通過采用深度學(xué)習(xí)算法,這些系統(tǒng)能夠?qū)W習(xí)和識別復(fù)雜的特征模式,從而準(zhǔn)確地檢測出各種類型的缺陷,如裂紋、腐蝕、變形等。
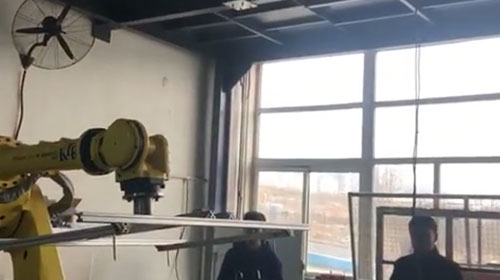
其次,在零部件缺陷檢測技術(shù)中,使用傳感器和設(shè)備收集大量的數(shù)據(jù)是關(guān)鍵。例如,紅外熱成像技術(shù)可以檢測零部件表面的溫度分布,以發(fā)現(xiàn)潛在的缺陷。同時,聲波傳感器和振動傳感器等技術(shù)也可以用于檢測隱蔽的缺陷。這些傳感器的數(shù)據(jù)可以與圖像數(shù)據(jù)相結(jié)合,通過多模態(tài)信息融合的方式提高檢測準(zhǔn)確性和魯棒性。
然而,盡管零部件缺陷檢測技術(shù)取得了顯著進展,仍然面臨一些挑戰(zhàn)。首先,不同類型的缺陷可能具有復(fù)雜的形態(tài)和變異性,因此算法需要具備較強的適應(yīng)性和泛化能力。其次,零部件的材料、幾何形狀和制造工藝等因素可能對檢測結(jié)果產(chǎn)生影響,因此算法需要具備一定的魯棒性。此外,在實際應(yīng)用中,大規(guī)模的數(shù)據(jù)集收集和標(biāo)注也是一個挑戰(zhàn),因為這需要耗費大量的時間和人力成本。
為了克服這些挑戰(zhàn),未來的研究可以從以下幾個方向進行探索。首先,進一步提升機器學(xué)習(xí)和深度學(xué)習(xí)算法的性能,優(yōu)化網(wǎng)絡(luò)結(jié)構(gòu)和訓(xùn)練策略,以提高缺陷檢測的準(zhǔn)確性和魯棒性。其次,引入更多的傳感器和信息源,如聲音、振動、紋理等,以提供更全面和多維度的數(shù)據(jù),增強系統(tǒng)對缺陷的感知能力。此外,還可以探索無監(jiān)督學(xué)習(xí)和自適應(yīng)學(xué)習(xí)等方法,以減少對大規(guī)模標(biāo)注數(shù)據(jù)的依賴。
總之,零部件缺陷檢測技術(shù)的進展為制造業(yè)帶來了巨大的機遇和挑戰(zhàn)。通過結(jié)合計算機視覺、機器學(xué)習(xí)和傳感器技術(shù),零部件缺陷檢測系統(tǒng)能夠?qū)崿F(xiàn)自動化、高效率和高精度的缺陷檢測。然而,仍然需要進一步研究和創(chuàng)新,以應(yīng)對各種復(fù)雜的生產(chǎn)場景和實際問題。只有不斷推動技術(shù)的發(fā)展和應(yīng)用,才能夠滿足制造業(yè)對高質(zhì)量產(chǎn)品的需求,提升企業(yè)競爭力。